An Application Class 3 (AC3) PROFIdrive device is a “Positioning Mode” drive, and it builds on the concepts of an AC1 device. However, instead of commanding a drive to move at a desired speed, now the controller asks the drive to move to a desired position. An AC3 device, as with AC1, handles all of the feedback from the positioning operation locally and keeps the controller informed of what it’s doing over the cyclic data interface. But as we’ll see, commanding a drive to move to a desired position is much more complex than simply commanding a rotational speed.
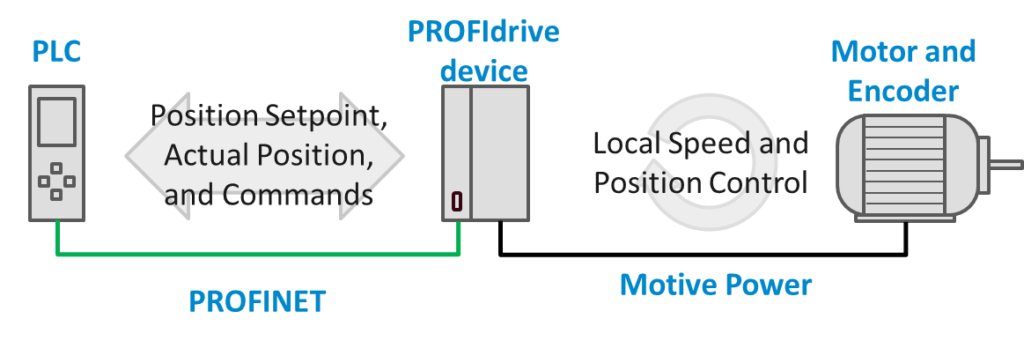
PROFIdrive Application Class 3 devices implement both position and speed control loops locally. This keeps communication with the PLC simple and possible over an unsynchronized PROFINET RT network.
Homing and Traversing
An AC3 PROFIdrive device has to handle more than the usual jogging and braking tasks of an AC1 device. It also has to have some sense of where the drive output has moved in the real world (homing), and know how to move it to a desired location without breaking anything (traversing). This means that the drive axis must deal with a number of motion parameters that aren’t used with speed control, like acceleration, deceleration, and position limitations.
There are two ways to communicate a position move with an AC3 PROFIdrive device, via the “Program” and “MDI” (Manual Data Input) telegrams. If you have a look in the PROFIdrive profile, these are Standard Telegrams 7 and 9, respectively.
Telegram Types
Program telegrams are short with only two bytes of input and output data. They tell the drive to execute one of a number of pre-programmed positioning moves that are stored in the drive during commissioning. Since all of the difficult programming work is done during that commissioning process, the controller only needs to send a reference to the move rather than send real data. Program telegrams must be supported by AC3 drives.
MDI telegrams are larger, with several variables to describe things like a target position, velocity, acceleration, deceleration, and direction. MDI telegrams are used when a controller needs to execute a positioning move that wasn’t stored in the drive during commissioning, or if a motion path is more complex than the drive can execute on its own. Because it’s harder to implement the MDI telegrams on both the controller and device, they’re optional for AC3 drives.
PROFIdrive without synchronization
Like AC1 drives, Application Class 3 drives can be implemented on PROFINET Conformance Class A, B, or C devices, and rely on the drive to provide internal control loops. With AC3, the PLC is only a gateway to a broader automation system, tying the PROFIdrive device to external sensors, actuators and HMIs. For synchronized positioning, drives must implement AC4 or other application classes.
Wrapping it up
PROFIdrive AC3 is useful for small, isolated positioning movements, and it can be used without special PROFINET Conformance Class 3 interfaces or synchronized applications. Like AC1, it’s a great way to implement PROFIdrive quickly on smaller motion controllers. But also like AC1, the lack of a synchronized network interface is a performance-limiting drawback in complex applications. If AC3 doesn’t work for your application, check out Application Class 4.